8 Steps to Create an Effective Preventive Action Plan
Learn how to create a preventive action plan to identify and mitigate facility risks, saving money and boosting safety.
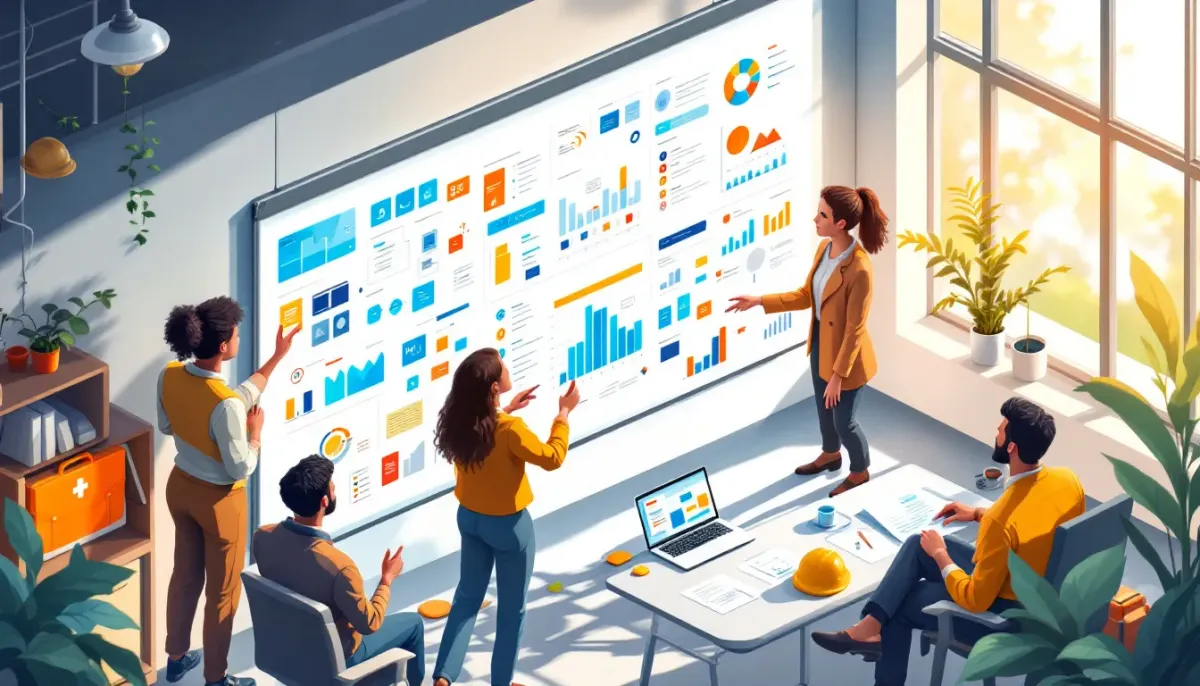
Want to stop problems before they start? Here's how to make a preventive action plan that works:
- Spot risks
- Rank them
- Plan prevention
- Assign tasks
- Set deadlines
- Get resources
- Take action
- Review and update
Why bother? A good plan:
- Saves money
- Boosts safety
- Keeps you legal
- Smooths operations
- Engages staff
Here's a quick look at common facility risks:
Risk Type | Examples |
---|---|
Health & Safety | Slips, falls, strain injuries |
Fire | Bad wiring, blocked exits |
Infrastructure | Power cuts, internet outages |
Security | Theft, unauthorized access |
Environmental | Chemical spills, wrong waste disposal |
Compliance | Breaking rules, missed inspections |
Ready to dive in? Let's get started on your preventive action plan.
1. Find possible risks
To create a solid preventive action plan, you need to spot potential problems in your facility. Here's how to do it and what to look out for.
Spotting risks
Here are some ways to identify risks:
- Walk around: Do regular checks of your workplace. Look for things like broken equipment or unsafe conditions.
- Check your history: Look at past accidents, near-misses, and complaints. You might see patterns.
- Ask your team: Your workers often know the risks best. Make it easy for them to report problems.
- Look at industry guides: Check out safety info from groups like the Health and Safety Executive (HSE).
- Use tools: Checklists and software can help you find hazards systematically.
Common risks
Here's what facility managers often deal with:
Risk Type | What it looks like |
---|---|
Health & Safety | Slips, falls, repetitive strain injuries |
Fire | Bad wiring, blocked fire exits |
Infrastructure | Power cuts, internet outages |
Security | Theft, people getting in who shouldn't |
Environmental | Chemical spills, wrong waste disposal |
Compliance | Breaking rules, missing inspections |
Risks can change. Think about how quickly facilities had to adapt to COVID-19 in March 2020.
"Finding workplace hazards is key to any good safety program. It's not just ticking boxes; it's about making everyone alert to risks", says John O'Toole from the British Safety Council.
2. Rank risks by importance
After spotting potential risks, you need to prioritise them. This helps you focus on what matters most.
Risk scoring methods
There are three main ways to measure risk severity:
- Qualitative: Uses simple terms like "high", "medium", "low". Quick but less precise.
- Quantitative: Uses numbers, often percentages or probabilities. More exact but time-consuming.
- Hybrid: Combines both for a balanced approach.
The Hazard Identification and Risk Ranking (HIRR) method is a useful tool. It guides you through hazard spotting and risk assessment step-by-step.
Create a risk chart
A risk chart (or matrix) visually shows which risks need urgent attention. Here's how to make one:
- List all identified risks.
- Score each risk based on likelihood and potential impact.
- Plot scores on a chart.
Here's a simple risk matrix:
Likelihood | Very Likely | Likely | Unlikely | Highly Unlikely |
---|---|---|---|---|
Fatality | High | High | High | Medium |
Major Injuries | High | High | Medium | Medium |
Minor Injuries | High | Medium | Medium | Low |
Negligible Injuries | Medium | Medium | Low | Low |
This chart helps you quickly spot high-priority risks.
"Large facilities lose an average of 27 hours a month due to equipment failure, costing about £532,000 for each hour of planned downtime."
This fact shows why ranking risks is crucial. By tackling the most serious risks first, you can avoid major losses and keep operations running smoothly.
3. Plan how to prevent risks
After ranking risks, it's time to create a plan to stop problems before they happen. Let's match actions to risks and work within your limits.
Match actions to risks
For each high-priority risk:
- List it from your risk chart
- Brainstorm prevention methods
- Pick the most effective and doable actions
Take "equipment failure" as an example. Your prevention actions might be:
- Regular maintenance schedule
- Staff training on proper equipment use
- Backup systems investment
Work within your limits
Consider your resources when planning:
- Budget: How much can you spend?
- Staff capacity: What time and skills are available?
- Prioritize: Focus on critical risks first
Resource | Consideration | Example |
---|---|---|
Budget | Prevention costs | £10,000 for new safety gear |
Staff | Available time/skills | 2 hours/week for equipment checks |
Equipment | Existing tools | Use current CMMS for scheduling |
It's better to do a few things well than spread yourself too thin.
"Being proactive rather than reactive is always the best approach to risk reduction." - AuditBoard
This quote nails it. Act now to avoid costly problems later.
Some quick tips:
- Use checklists for consistent inspections
- Try a digital maintenance system for tracking and reminders
- Encourage staff to report small issues
- Get employees involved in maintenance planning
4. Assign tasks to people
Picking the right people for tasks is key to a solid preventive action plan. Here's how to do it:
Choose who's in charge
When building your team:
- Match skills to tasks
- Check workload and availability
- Look for relevant experience
For a new equipment maintenance schedule, you might pick:
- A senior tech to lead
- Experienced operators for checks
- An IT pro for digital tracking
Set up ways to talk
Good communication is a must. Try these:
- Use Trello or Asana for project management
- Have weekly team meetings
- Create a Slack channel for quick updates
"Delegation isn't just about handing out tasks. It's about empowering your team, using their strengths, and building ownership." - Gather Vacations
Put this into action with a RACI matrix:
Task | Responsible | Accountable | Consulted | Informed |
---|---|---|---|---|
Risk assessment | Safety Officer | Facility Manager | Department Heads | All Staff |
Equipment checks | Maintenance Team | Chief Engineer | Equipment Suppliers | Operators |
Staff training | HR Manager | Operations Director | Training Provider | All Staff |
This table shows who does what, who decides, who to ask, and who to tell.
5. Set deadlines
Setting clear deadlines is crucial for your preventive action plan. Here's how to do it:
Make a timeline
Break your plan into smaller tasks and set specific finish dates for each. Be realistic with your timelines - tight enough to keep focus, but not so tight that they're impossible to meet.
A Gantt chart can help visualize task overlaps and dependencies. Here's a simple example for a fire safety upgrade:
Task | Week 1 | Week 2 | Week 3 | Week 4 | Week 5 |
---|---|---|---|---|---|
Risk assessment | X | X | |||
Order equipment | X | ||||
Install alarms | X | X | |||
Staff training | X | X | |||
Final checks | X |
Set milestones to track progress and celebrate wins. Add buffer time for unexpected delays. Get your team's buy-in on the timeline - they're the ones making it happen.
Review progress weekly and adjust deadlines if needed, but always explain why.
"Unrealistic deadlines. They create anxiety and place operational teams under pressure which can lead to one task taking an entire team away from critical aspects conducted by the FM team as a part of their daily business as usual." - Kelly Wallace, Facilities Manager for Macquarie Group.
Remember: Unrealistic deadlines can derail your entire plan. Balance ambition with practicality to keep your team focused and on track.
6. Get needed resources
To implement your preventive action plan, you'll need the right resources. Let's look at budgeting and staffing.
Plan your budget
Figure out the costs for each prevention task. Don't miss anything - overlooked expenses can throw off your plan.
Here's a basic budget template:
Item | Cost | Quantity | Total |
---|---|---|---|
Fire alarms | £50 | 10 | £500 |
Staff training | £200 | 5 | £1000 |
Safety signs | £10 | 20 | £200 |
Emergency kits | £75 | 5 | £375 |
Total | £2075 |
Add a 10-15% buffer for unexpected costs.
Staff and train people
Determine who you need to execute your plan:
- Number of people
- Required skills
- Necessary training
Training is crucial. It helps your team identify risks and respond quickly to issues.
"Ensuring health and safety in the workplace is a challenging but not impossible task. It begins with a culture where employees are taught and feel empowered to act and behave in a safe way." - Darrell X. Rounds, Electrical and Mechanical Engineering Lead, General Motors' Facilities Organisation.
Training tips:
- Hold regular sessions
- Use hands-on drills and simulations
- Customize training for different roles
- Track who's been trained and when
Effective training doesn't just check a box. It builds a safety-first culture that prevents many risks before they happen.
7. Put the plan into action
It's time to roll out your preventive action plan. This is where the rubber meets the road.
Kickstarting the process
- Spread the word: Brief your team on the new plan. Make it clear why it matters.
- Delegate responsibilities: Use your QMS software to assign tasks. Everyone should know their role.
- Open communication channels: Set up a system for feedback during the rollout. A suggestion box or regular check-ins work well.
- Launch training: Start educating your team on new safety measures. Hands-on practice is key.
Monitor progress
Once your plan is live, keep tabs on it:
- Crunch the numbers: Track safety incidents before and after implementation. If you're targeting falls, compare the frequency.
- Conduct spot checks: Drop in unannounced to see if new rules are being followed.
- Gather input: Chat with your team about the plan's effectiveness. They might spot issues you've missed.
- Document everything: Note what's working and what's not. This info is gold for future updates.
Don't sweat it if your plan isn't perfect right off the bat. Tweaks are often needed. It's all part of creating a safer workplace.
8. Check and update the plan
Your preventive action plan needs regular check-ups to stay effective.
Set review times
Schedule regular reviews:
- Monthly: Check key safety metrics
- Quarterly: Analyse trends in your data
- Annually: Do a top-to-bottom review
Put these in your calendar. Treat them like any other important meeting.
Keep improving
Use what you learn:
1. Ask your team
Get feedback from the front lines. What's working? What isn't?
2. Look at the numbers
Are incident rates down since you started the plan?
3. Stay current
Keep an eye on new safety rules and industry best practices.
4. Try new things
If something's not working, switch it up. Don't be scared to experiment.
Improving your plan is ongoing. It's about small, steady changes over time.
"Manufacturers should consider that their corrective action and preventive action documentation can demonstrate to FDA that the manufacturer's quality system is effective and enables the manufacturer to identify problems quickly and implement effective corrective and preventive actions (or not)." - Brian Dense, Quality Systems Expert.
Conclusion
Let's recap how to create an effective preventive action plan for managing facility risks:
- Spot potential issues early
- Prioritize the biggest concerns
- Match specific actions to each risk
- Assign clear roles to team members
- Set deadlines for each task
- Secure necessary resources
- Start small and monitor progress
- Keep improving your plan
A solid preventive action plan pays off:
1. Saves money: Stopping problems early costs less than fixing them later.
2. Boosts safety: Regular checks mean fewer accidents.
3. Keeps you compliant: You'll stay on top of regulations.
4. Smooths operations: Tackling risks improves your processes.
5. Engages staff: Team members feel more involved in prevention.
"Corrective and preventive action documentation shows FDA how effective a manufacturer's quality system is at quickly identifying and addressing problems." - Brian Dense, Quality Systems Expert
FAQs
How to make a preventive action plan?
Here's how to create a solid preventive action plan:
- Spot potential issues and their causes
- Focus on the most pressing risks first
- Outline specific steps to tackle each risk
- Assign tasks to your team
- Set a timeline for action
- Make sure you have the right tools and budget
- Put your plan into action
- Keep an eye on progress and tweak as needed
Pro tip: Use the Plan-Do-Check-Act cycle to keep improving your approach.
How do you write a preventive action plan?
When putting your preventive action plan on paper, include:
- A clear breakdown of risks and their potential impact
- Specific actions to address each risk
- Who's responsible for what
- Deadlines for each preventive measure
- Resources needed (money, people, tools)
- How you'll track progress
- When management will review the plan's effectiveness
Be thorough in your documentation. It'll help keep everyone on the same page and accountable.
Remember: Your plan isn't set in stone. Regular reviews by management will help you see what's working and what needs to change.