Equipment Allocation in Facilities Management: Guide
Discover essential strategies for effective equipment allocation in facilities management to enhance productivity and reduce costs.
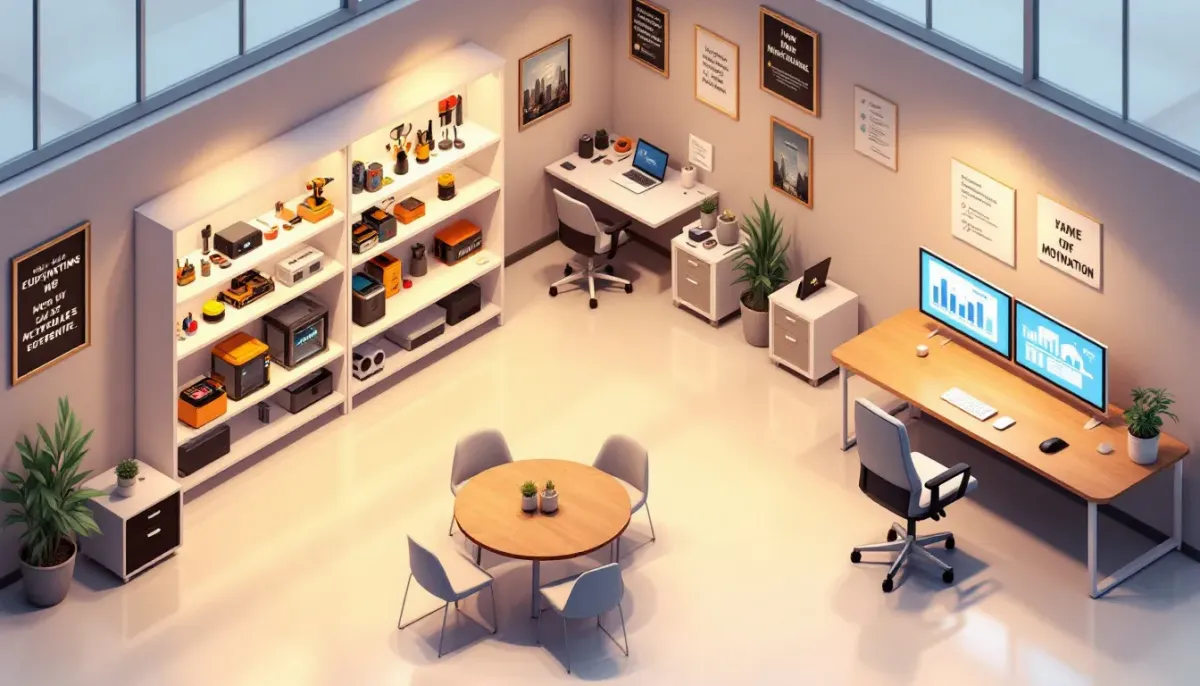
Here's what you need to know about equipment allocation in facilities management:
- It's about getting the right tools to the right places at the right times
- Good allocation saves money, keeps people safe, and boosts productivity
- Key steps:
- Do regular equipment audits
- Match equipment to tasks
- Track usage patterns
- Prioritise based on criticality
- Use technology like CMMS to help
- Create clear allocation procedures
- Train staff on proper use
- Review and improve regularly
Common challenges and solutions:
Challenge | Solution |
---|---|
Equipment shortages | Prioritise needs, use tracking software |
Conflicting requests | Rank urgency, use booking systems |
Equipment misuse | Train staff, implement check-in/out system |
Remember: Better allocation means smoother operations and happier teams. Keep improving your system to stay ahead.
Basics of Equipment Allocation
Equipment allocation in facilities management is about getting the right tools to the right places at the right times. Let's look at common equipment types and key allocation principles.
Common Facility Equipment Types
Facility managers handle various equipment types:
Equipment Category | Examples |
---|---|
Office Equipment | Computers, printers, scanners, phones |
Building Systems | HVAC, security systems, fire safety systems |
Maintenance Tools | Industrial cleaning equipment, power tools, saws |
Safety Gear | Fire extinguishers, goggles, respirators |
Specialised Equipment | X-ray machines (hospitals), kitchen appliances (food service) |
Core Allocation Principles
To allocate equipment effectively:
1. Match equipment to tasks
Ensure you have the right tools for each job. For example, put X-ray machines in the right hospital wards, not randomly scattered.
2. Track usage patterns
Monitor when and how often equipment is used. This helps prevent expensive kit sitting idle in one area while another department is short.
3. Prioritise based on criticality
Some equipment is more crucial than others. Use a criticality matrix to identify must-have tools for keeping your business running.
4. Balance efficiency and cost
Find the sweet spot between having enough equipment and not wasting money on excess.
5. Use technology to help
Use a Computerized Maintenance Management System (CMMS) to track equipment location and maintenance needs.
"A CMMS is essential for managing equipment maintenance, including tracking asset information, scheduling preventive maintenance, and managing work orders", says the International Facility Management Association (IFMA).
6. Keep it safe and legal
Follow all rules and safety standards. This keeps people safe and avoids costly fines.
7. Plan for the unexpected
Have a system for equipment breakdowns or sudden high demand. Consider backup equipment or quick ways to move tools between departments.
Checking Equipment Needs
To make smart decisions about equipment, you need to know what you've got and what you need. Here's how:
Equipment Audit
Start by taking stock:
- List all equipment
- Note condition, age, and usage
- Check maintenance status
- Spot gaps or redundancies
Use a CMMS to track this info. It's faster and more accurate.
Must-Have Equipment
Some items are critical. To spot these:
- Look at core business functions
- Check regulations
- Consider safety needs
For example, a hospital needs life support systems and sterilisation equipment.
Usage Patterns
Understanding how equipment is used helps you allocate it better:
Metric | Why It Matters |
---|---|
Use frequency | Shows high-demand items |
Use duration | Helps plan maintenance |
Peak times | Guides scheduling |
Idle time | Spots underused equipment |
Here's a real-world example:
"By analysing our equipment data, we cut forklift idle time by 30% and saved £50,000 in rentals last year", says Tom Brown, Facilities Manager at XYZ Manufacturing.
Tracking usage can lead to big savings. It's worth the effort.
Making an Allocation Plan
Here's how to create an equipment allocation plan that meets your goals and budget:
Setting Priorities
Rank your equipment's importance:
- List all equipment
- Score each item (1-5) based on:
- Usage frequency
- Operational impact
- Safety requirements
- Legal compliance
Balancing Efficiency and Cost
To find the sweet spot between productivity and cost:
- Analyze equipment usage data
- Boost efficiency
- Share equipment between teams
- Consider renting vs buying for less-used items
Following Rules and Safety Standards
Put safety first:
- Know relevant safety laws
- Ensure equipment meets standards
- Train staff properly
- Keep maintenance records
Example: Maintenance Risk Matrix
Use this to prioritize equipment attention:
Risk Level | Impact on Operations | Safety Risk | Action Needed |
---|---|---|---|
High | Stops work | Could cause injury | Fix immediately |
Medium | Slows work | Minor safety issue | Plan to fix soon |
Low | Little impact | No safety risk | Fix when possible |
Example: A broken safety switch? That's high risk. Fix it NOW.
Setting Up an Allocation System
A clear system is key for managing equipment allocation. Here's how to set one up:
Picking Allocation Methods
Choose a method that fits your needs:
Method | Description | Best for |
---|---|---|
First-come, first-served | First requester gets the equipment | Small teams, low-demand items |
Priority-based | Job importance determines allocation | Critical ops, limited resources |
Rotation | Shared on a schedule | Teams with similar needs, high-demand items |
Needs-based | Given based on project requirements | Diverse teams, specialised equipment |
Creating Clear Procedures
Your procedures should cover:
- How to submit requests
- Who approves them
- Equipment collection and return
- Usage rules
- What to do if something breaks
Making a Request and Approval Process
Set up a simple system:
1. Create a request form
Include:
- Equipment name
- Request reason
- Needed date
- Expected return date
2. Set up approval steps
Example:
- Team leader review
- Facilities manager availability check
- Department head final approval
3. Use tech to streamline
The HVI APP can help you:
- Track equipment usage
- See due dates
- Get overdue alerts
4. Train staff
Regular training helps reduce mistakes and misuse.
Using Technology for Allocation
Equipment management software makes tool tracking and allocation a breeze. Here's how to use tech to your advantage:
Equipment Management Software Basics
Modern software takes the headache out of tool management. It offers:
- Real-time equipment tracking
- Automated maintenance schedules
- Easy check-in/check-out
- Data-driven allocation insights
Key Software Features to Look For
When shopping for equipment management software, keep an eye out for:
Feature | What It Does |
---|---|
Asset tracking | Shows where your stuff is and if it's working |
Work order management | Handles maintenance requests |
Inventory management | Keeps tabs on stock |
Reporting and analytics | Gives you the lowdown on equipment use |
Mobile access | Lets staff update info on the go |
Integration capabilities | Plays nice with other systems |
Using Barcodes or RFID for Tracking
Barcodes and RFID tags make tracking a snap:
Barcodes:
- Cheap and cheerful
- Need line-of-sight
- Great for indoor use and smaller items
RFID:
- Pricier but more powerful
- No line-of-sight needed
- Works outdoors and on bigger equipment
A construction company slapped RFID tags on their pricey tools. Result? 80% less theft and £250,000 saved in just one year.
"RFID tool tracking saved us up to £1 million in potential losses." - Construction Industry Report
Want to give it a go? Here's how:
- Pick barcodes or RFID
- Tag your equipment
- Set up scanning spots
- Train your team
- Keep your database up to date
Tips for Better Equipment Allocation
Here's how to step up your equipment allocation game:
Regular Equipment Maintenance
Keep your gear in shape:
- Check equipment based on maker's advice
- Teach staff to spot problems early
- Use software to track maintenance
"Preventative maintenance stops costly breakdowns and downtime." - RedBeam Software
Training Staff on Equipment Use
Good training cuts misuse and boosts efficiency:
- Give hands-on training to new hires
- Pair new staff with experienced ones
- Make simple guides for each tool
Using a Check-in/Check-out System
Track your tools like a pro:
System | Pros | Cons |
---|---|---|
Digital | Live updates, easy reports | Costs more |
Manual | Cheap, simple to set up | Slow, more mistakes |
"I used to use a clipboard for signing out gear. Now, I'd go digital. It's faster and more accurate." - Construction Tool Management Expert
Reviewing Allocation Regularly
Keep your methods sharp:
- Do monthly checks to see usage trends
- Change allocation based on needs and performance
- Ask staff for feedback
Common Allocation Problems and Solutions
Handling Equipment Shortages
Equipment shortages can mess up your day. Here's how to deal:
- Make a priority list. Who needs what most?
- Use software to track your gear.
- Look at past use to predict future needs.
Solving Conflicting Requests
When everyone wants the same stuff:
Do This | Why It Works |
---|---|
Rank requests | Helps you decide what's urgent |
Use a booking system | Lets staff plan ahead |
Stagger schedules | Spreads out equipment use |
Stopping Equipment Misuse
Misuse leads to breakdowns and costs. Here's how to stop it:
1. Train your team
Show them how to use tools right. Make safety a big deal.
2. Track who's using what
Set up a check-in/check-out system. It keeps people honest.
3. Do surprise checks
Pop in and make sure gear's where it should be and used properly.
Did you know? If workers spend just 10 minutes a day looking for tools, that's 43 hours a year gone. That's like losing two whole workdays!
Checking and Improving Allocation
Want to boost your equipment allocation? Here's how to measure and improve it:
Key Allocation Metrics
Keep an eye on these numbers:
Metric | Measures | Why It's Important |
---|---|---|
Equipment Availability | % of time gear's ready to use | Shows if you've got enough |
Mean Time Between Failures | Average time between breakdowns | Tells you about reliability |
Mean Time to Repair | Average fix time | Shows repair speed |
Utilisation Rate | How often gear's used | Spots underused equipment |
Gathering and Using Data
Smart choices come from good data. Here's what to do:
1. Use tracking software
Get a system that logs equipment use, maintenance, and location. It'll cut mistakes and give you a clear picture.
2. Set up regular audits
Check your gear every few months. It keeps records fresh and catches issues early.
3. Look at the numbers
Review your metrics often. Spot problems like unused gear or frequent breakdowns? Fix them fast.
Keep Improving
Always aim higher:
- Train your team on proper use and tracking
- Update old, breakdown-prone gear
- Use barcodes or RFID for faster, more accurate tracking
- Ask your team for feedback - they might have great ideas
Remember: Better allocation means smoother operations and happier teams. Keep at it!
Real Example: Successful Equipment Allocation
Case Study: Jon Corns and the Industrial Equipment Manufacturer
Jon Corns stepped in as interim Managing Director for an industrial equipment manufacturer in trouble. The company was struggling with market downturns, high costs, and a lack of structure.
Here's how Corns turned things around:
- He made a clear plan, focusing on where to best use the company's gear.
- He set up ways to measure how well equipment was being used.
- He made sure everyone knew their job and what they were responsible for.
- He streamlined work processes, cutting waste and boosting output.
- He found ways different parts of the business could work together and share resources.
- He set up the company to handle future changes.
The results were impressive:
Metric | Improvement |
---|---|
Revenue | Up 11% |
Gross Profit | Up 27% |
EBITDA | Up 609% |
Overheads | Down 8% |
What We Learned
This case offers key insights for facilities managers:
- Plan ahead with a solid strategy.
- Measure everything - you can't improve what you don't track.
- Make sure people know their roles for efficient equipment use.
- Always look for ways to improve your processes.
- Think long-term and plan for future needs.
- Use data to guide your resource allocation decisions.
Conclusion
Equipment allocation in facilities management isn't easy. But get it right, and you'll see big benefits. Here's what you need to know:
- Do regular equipment checks
- Make a solid allocation plan
- Use tech to make things easier
- Keep equipment in good shape and train your staff
- Always look for ways to improve
What's Coming Next?
The world of equipment allocation is changing fast. Here's what's on the horizon:
1. AI and IoT are coming
These tech giants are set to shake things up. They'll help:
- Spot when equipment needs fixing before it breaks
- Use resources better
- Do the boring allocation stuff automatically
2. Going green is in
Everyone's talking about sustainability. Here's why it matters:
What You Can Do | Why It's Good |
---|---|
Switch to LED lights | Uses half the power |
Get energy-smart equipment | Smaller carbon footprint |
Install smart building tech | Uses less energy overall |
3. Data is king
More companies are using data to make smart choices. As Graham Perry puts it:
"By embracing advanced analytics now, you're not just solving today's problems – you're future-proofing your organisation for the challenges of tomorrow."
4. Fix it before it breaks
Say goodbye to fixing things when they break. Hello to fixing them before they do. Why? In car plants, one hour of surprise downtime costs over £2 million. Ouch.