Inventory Tracking Systems: Complete Guide 2024
Discover the essentials of inventory tracking systems, their benefits, types, and the latest trends for 2024 to optimise your business operations.
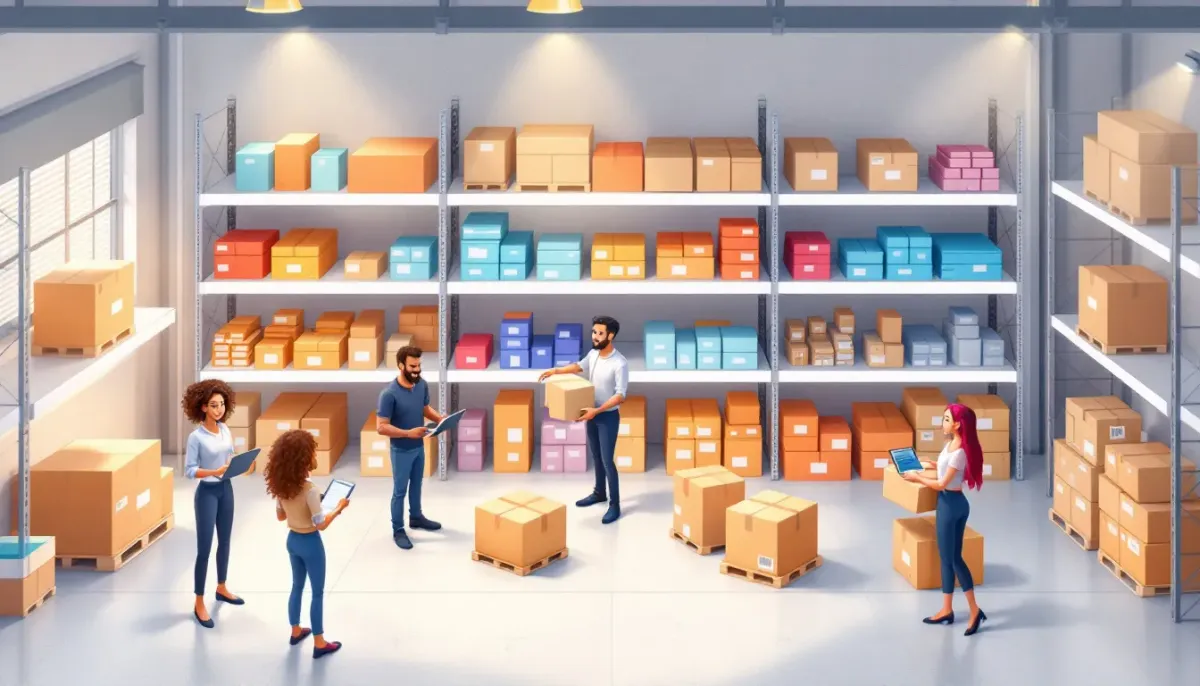
Inventory tracking systems are essential tools for modern businesses to monitor stock levels, locations, and movements in real-time. Here's what you need to know:
- Definition: Software and hardware setups that watch stock from raw materials to finished products
- Importance: Saves money, keeps customers happy, aids smart buying decisions
- Key components: Software, hardware, database, user interface, reporting tools
- Types: Manual, barcode, RFID, IoT-based
- Benefits: Better accuracy, real-time info, cost savings, smarter decisions, improved customer satisfaction
- Choosing a system: Consider your needs, scalability, integrations, ease of use, and budget
- Setup process: Prepare data, migrate carefully, train staff thoroughly
- 2024 trends: AI and machine learning, blockchain, cloud systems, mobile access
Feature | Benefit |
---|---|
Real-time tracking | Instant stock level updates |
AI forecasting | Optimised inventory levels |
Cloud-based | Access from anywhere |
Mobile apps | On-the-go management |
Integration | Syncs with other business tools |
Implementing a good inventory tracking system can slash costs, boost efficiency, and improve customer satisfaction. As technology evolves, staying updated with the latest trends will help businesses maintain a competitive edge in inventory management.
Basics of inventory tracking systems
Main parts of inventory tracking systems
Inventory tracking systems have five key parts:
- Software: The system's brain
- Hardware: Scanners and readers for data input
- Database: Stores all inventory info
- User interface: How staff use the system
- Reporting tools: Turn data into insights
Different types of tracking systems
Here's a quick look at the main types:
System Type | What it is | Who it's for |
---|---|---|
Manual | Paper or spreadsheets | Small businesses, few items |
Barcode | Scans barcodes | Medium-sized businesses |
RFID | Wireless tracking | Large businesses, high-value items |
IoT-based | Uses sensors | Businesses needing constant monitoring |
Features of current tracking systems
Today's systems pack a punch:
- They update in real-time
- Track across multiple locations
- Reorder automatically
- Play nice with other business software
- Let you check stock on your phone
Take Hickory Farms, for example. They use Microsoft Dynamics 365 to keep tabs on their entire supply chain. It's a lifesaver during their busy season when their team balloons.
Advantages of using tracking systems
Inventory tracking systems pack a punch for businesses. Here's how they boost operations and cut costs:
Better accuracy and efficiency
These systems slash errors and speed things up. How?
- Barcodes or RFID tags log items fast and accurately
- Less manual data entry
- Quicker order processing
Take Peta + Jain, a vegan clothing brand. They saved £104,000 yearly by automating order processing and shipping labels.
Real-time inventory info
Live tracking keeps stock data fresh. This means:
- Knowing exact stock levels anytime
- No more selling unavailable items
- Spotting low stock before it's too late
Money in the bank
Good tracking = cost savings:
Area | Benefit |
---|---|
Less overstock | Lower storage and insurance costs |
Fewer stockouts | No lost sales |
Lower labour costs | Automation of manual tasks |
Wholesale distributors using these systems? They've slashed inventory costs by 30% on average.
Smarter decisions
Accurate data helps businesses nail:
- Reorder timing
- Best-selling products
- Optimal inventory levels
Ian Hobkirk, President at Commonwealth Supply Chain Advisors, says:
"By effectively removing the 'emotional' component of inventory management, and by putting real data and insights into the warehouse manager's hands, these solutions enable a more streamlined, reliable inventory management approach."
Customer satisfaction boost
Keeping the right stock means:
- Faster order fulfilment
- Fewer "out of stock" letdowns
- More repeat business
Accurate orders = happy customers = loyalty and repeat purchases.
Picking the right tracking system
Choosing an inventory tracking system? It's a big deal. Here's how to nail it:
Know your needs
First up, figure out what you actually need:
- How many products?
- Multiple locations?
- Current inventory headaches?
A small shop might just need basic counting. A big warehouse? Real-time tracking and auto-reordering.
Think big
Don't box yourself in. Pick a system that can grow with you. LedgerGurus puts it bluntly:
"We have seen MULTIPLE companies reach a point of desperation and spend many tens of thousands implementing an ERP way before they needed one because they went cheap on inventory tools or never implemented one at all."
Ouch. Look for scalable features and flexible pricing tiers.
Play nice with others
Your new system needs to get along with your current tech. Check if it integrates with:
- Your online store
- Accounting software
- Shipping stuff
Using Shopify? Make sure your inventory system talks to it. No one likes double data entry.
Keep it simple
If your team can't use it, it's useless. Look for:
- Clean, intuitive interfaces
- Clear processes
- Solid training resources
Try before you buy. Most offer free demos.
Money matters
Prices vary. A lot. Here's a quick look:
Software | Price Range (Monthly) |
---|---|
Cin7 | Starts at £349 |
Ordoro | Free - £349 |
inFlow | £89 - £439 |
Zoho Inventory | Free - £249 |
Don't forget extra costs:
- Setup
- Training
- Hardware (like barcode scanners)
Think long-term. A good system pays for itself by cutting errors and boosting efficiency.
Take your time. Test drive a few options. Get your team's input. The right choice will streamline your ops and set you up for success.
Setting up your tracking system
Ready to get your new inventory tracking system going? Here's how:
Getting ready
Before you start:
- List your products and where they are
- Look at how you do things now
- Spot any issues
This helps you set up the new system to fix old problems.
Moving your data
Transferring your inventory info is a big task. Here's how:
1. Clean up your data
Go through your records. Fix errors. Remove duplicates.
2. Map your data
Match your old categories to the new system's fields. This helps avoid mix-ups.
3. Test run
Move a small batch of data first. Check for issues before doing the full transfer.
4. Full migration
Once you're happy with the test, move everything over. Double-check all info has transferred correctly.
Training your team
Your new system is only as good as the people using it. Here's how to train your team:
- Start with the basics. Show main features first.
- Use real examples from your business.
- Set up a practice area where staff can try without worry.
- Make quick guides for common tasks.
"Review the system and process with your team, including new hires. Keep initial training to 60 minutes max to help your team remember better."
All at once or step-by-step
You've got two main options for rolling out your new system:
Approach | Pros | Cons |
---|---|---|
All at once | Fast switch | More disruptive |
Step-by-step | Less overwhelming | Takes longer |
Most businesses do better with a step-by-step approach. Start with one product line or department, then grow.
Common problems and fixes
Even with good planning, you might hit some snags:
- Numbers don't match: Do a physical count to check.
- Staff push back: Show how the new system makes their job easier.
- System acts up: Keep your vendor's support number handy.
New features in 2024
Inventory tracking is getting a major upgrade. Here's what's hot for 2024:
AI and machine learning
AI is revolutionizing stock management. It crunches data on past sales, market trends, and more to forecast future needs. The result?
- Spot-on stock levels
- Less cash tied up in excess inventory
- Fewer stockouts
Take Walmart. Their AI system keeps shelves stocked by analyzing sales patterns and supplier performance.
Smarter predictions
AI doesn't just look back—it spots hidden patterns and plans ahead. This is huge for:
- Seasonal items
- New product rollouts
- Supply chain hiccups
Amazon's AI can predict your order before you click "buy", ensuring lightning-fast shipping.
Blockchain tracking
Blockchain isn't just crypto-talk anymore. It's shaking up inventory tracking:
- Creates tamper-proof records
- Gives everyone in the supply chain the same view
- Fights fraud and counterfeits
Mitsubishi Chemical Group tested blockchain to track materials from start to finish, distinguishing recycled from new.
Cloud systems
Cloud-based tracking is pushing out old-school software. Why? It offers:
- Access from anywhere
- Real-time updates for all users
- Easy scaling as you grow
Tookstock, for example, lets you check stock and spot trends from any device.
Mobile access
Checking stock from your phone? Game-changer. It means:
- On-the-go updates by warehouse staff
- Managers can check levels anytime, anywhere
- Faster problem-solving
Most new systems now come with mobile apps, keeping everyone in sync.
These features are making inventory tracking faster, more precise, and user-friendly. Embracing these tools can slash costs and boost customer satisfaction through better stock management.
Tracking systems in different industries
Inventory tracking isn't one-size-fits-all. Let's see how various sectors use these systems to boost their operations.
Retail tracking
Retailers NEED to know what's on their shelves. Here's why:
- Tesco's RFID tags for clothes? 4% fewer stockouts and more sales.
- Walmart's AI crunches numbers to keep shelves full.
These systems help shops spot trends, update stock in real-time, and cut waste.
Factory inventory management
Factories juggle raw materials, work-in-progress, and finished goods. Enter Just-in-Time (JIT) inventory:
Toyota only orders parts when needed. Result? Less warehouse space, lower costs, and smoother production.
Healthcare supply tracking
Hospitals can't afford to run out of supplies. Good tracking systems:
- Keep critical items stocked
- Manage expiry dates
- Help meet regulations
57% of healthcare workers remember times when doctors didn't have the right supplies. Yikes.
St. Mary's Hospital in London uses barcode scanning for meds. It updates inventory instantly, cuts counting errors, and helps prevent theft.
Warehouse management
Warehouses need to track items across HUGE spaces. Their systems offer:
- Real-time stock updates
- Support for barcodes and RFID
- Integration with other business tools
Amazon's fulfilment centres? Robots and AI track millions of items. They find and ship stuff fast, make the most of storage space, and slash picking errors.
In short: Good tracking = smoother operations, no matter the industry.
Tips for better inventory tracking
Want to keep your inventory in check? Here's how:
Regular stock checks
Count your stock often. It stops small errors from becoming big problems.
- Do cycle counting. Check some stock daily instead of shutting down for a full count.
- Focus on what matters. Count your most important items more often.
- Record problems right away. Note any damages or missing items as they happen.
Setting goals and measuring success
You need clear targets to know if your system's working:
- Track your sell-through rate (STR). It shows how fast you're selling.
- Watch your return rate. High returns might mean quality issues.
- Check your perfect order rate. It tells you how often orders go out without problems.
Always improving
Your inventory system should grow with your business:
- Train your team often. Everyone needs to know the latest best practices.
- Look for bottlenecks. Find and fix process problems.
- Keep up with tech. New tools might help you track better.
Keeping data safe
Your inventory data is valuable. Protect it:
- Use strong passwords. Change them often and keep them private.
- Back up your data. Keep copies in case something goes wrong.
- Control access. Only give people the info they need to do their job.
What's next for inventory tracking
Inventory tracking is changing fast. Here's what's coming:
New technology
AI and machine learning will transform stock tracking:
- AI will predict what you need to stock based on sales, trends, and even weather.
- Systems will automatically order when stock is low.
- Staff might ask chatbots about stock levels instead of checking computers.
Eco-friendly tracking
Inventory is going green:
- More businesses are switching to digital records.
- Companies are grouping orders to reduce deliveries.
- Buying from nearby suppliers cuts shipping miles.
Some shops now use digital price tags, updating quickly without wasting paper.
Connecting with other business systems
Inventory tracking will work with other parts of your business:
- Stock counts will update instantly when items sell.
- Staff can check stock while talking to customers.
- You'll know where your stock is from factory to shelf.
System | Benefit |
---|---|
Sales | Instant updates |
Customer Service | Quick checks |
Delivery | Full visibility |
Robert Connors, CEO of Gexpro Services, says:
"We set up 700 eTurns SensorBins at a powergen maker in Ohio. The customer cut stock by nearly $1M and got real-time inventory data."
This shows how new tech can boost a company's bottom line.
As we approach 2024, these changes will help businesses save money, work better, and keep customers happy. Stay ready to use new tools as they come out.
Real examples
Success stories
Let's look at how some companies boosted their operations by updating their inventory tracking:
Andretti Global (racing team):
- Better control of expensive car parts
- Less waste
- Faster pit stops
Teyssa Seed Research (Argentine biotech):
- No more manual data entry
- Improved budget forecasts
- Streamlined daily tasks
Her Jewellery Pte Ltd (Singapore jewellery maker):
- Smoother team workflow
- Easier multi-country stock management
- Quicker market response
Lessons learned
These stories highlight key points about inventory tracking:
1. Tailor your system
Each business needs its own approach. For instance:
- Marygrove Awnings: Keeps months of stock
- Amazon: Uses just-in-time delivery to cut storage costs
2. Use tech wisely
New tools can make a big impact:
Company | Tech used | Benefit |
---|---|---|
Gap | iOS devices | In-store ordering for out-of-stock items |
Countdown NZ | Compass app | Real-time sales tracking for suppliers |
3. Think beyond stock levels
Good systems do more than count:
- Erickson Living: Prices 20,000 flats in minutes
- Texas Tech Uni's Media College: Tracks equipment use and maintenance
4. Keep it simple
Even small teams can win big. Pet Ultra, a two-person online pet shop, uses tracking to:
- Know current stock
- Avoid overselling
- Plan restocks
John Moss, CEO of English Blinds, says:
"We mix computer predictions and human checks to manage stock. This helps us meet demand without getting stuck with hard-to-sell goods."
Wrap-up
Key takeaways
In 2024, inventory tracking systems are a MUST for businesses. Here's the scoop:
- Real-time tracking keeps you on top of stock levels
- AI and machine learning boost forecasting and optimisation
- Cloud solutions make data sharing a breeze
- Top systems play nice with your other business tools
- Options for every budget, from free to fancy
Software | Starting Price (Monthly) |
---|---|
Zoho Inventory | £29 |
Ordoro | £59 |
Katana | £179 |
Cin7 | £349 |
Looking ahead
The future of inventory tracking? It's all about tech:
- IoT devices will track stock in real-time
- Blockchain might make records more secure
- Green practices are on the rise
- Robots and AI could run the warehouse show
Bottom line: Stay sharp and keep an eye on these trends. Your inventory (and your bottom line) will thank you.
FAQs
What is inventory in facilities management?
In facilities management, inventory is all about the stuff you need to keep things running smoothly. We're talking:
- Cleaning supplies
- Maintenance tools
- Spare parts
- Office supplies
As a facilities manager, you've got to:
- Buy this stuff
- Keep track of it
- Set up a system to reorder when you're running low
Why bother? Simple: good inventory management keeps your facility ticking along without any hiccups.
How to choose an inventory management system?
Picking the right inventory management system isn't rocket science, but it's important. Here's what to look at:
Factor | What it means |
---|---|
Timing | Know when spreadsheets just aren't cutting it anymore |
Integrations | Figure out what other systems it needs to play nice with |
Features | Pin down what you actually need it to do |
Ease of use | Make sure it won't give your team a headache |
Support | Check if help is there when you need it |
Development | Think about whether it can grow with your business |
Get this right, and you could see some big wins. Just ask Oleg Twisto, a retailer who said: "After six months of using Kladana, I started selling 300 goods, and the turnover increased from $23,000 up to $57,000."
It's not just about sales, either. Tanat Sarsembay from Metako Steel Doors Production found an unexpected benefit: "Kladana stopped the theft in our company. When we switched to Kladana, many facts about dishonest employees came to light."
So, take your time. Find a system that fits like a glove. It could make your life a whole lot easier - and your business a whole lot more profitable.