Reactive vs Planned Maintenance: Pros, Cons, Differences
Explore the pros and cons of reactive vs planned maintenance, their impact on costs, downtime, and equipment lifespan, and find the best strategy for your business.
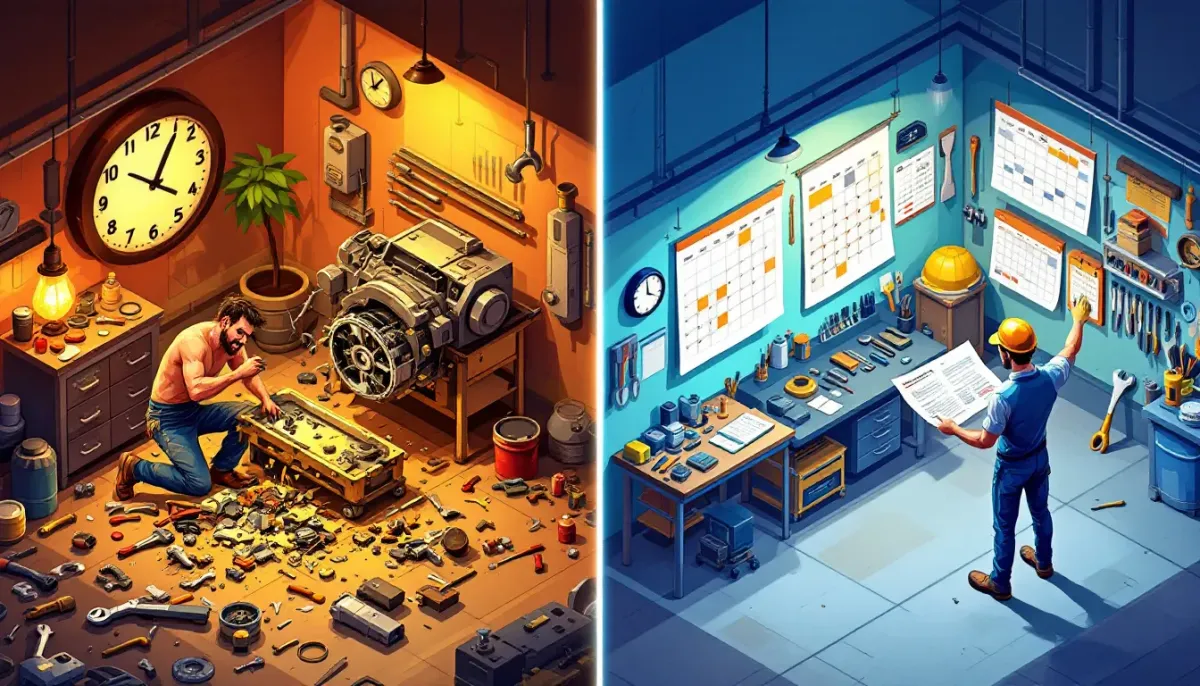
Reactive maintenance fixes things when they break. Planned maintenance prevents breakdowns through regular checks.
Key differences:
Aspect | Reactive Maintenance | Planned Maintenance |
---|---|---|
Timing | Fix when broken | Scheduled in advance |
Cost | Low upfront, high long-term | High upfront, low long-term |
Downtime | Unpredictable, often long | Minimal, scheduled |
Asset lifespan | Shorter | Longer |
Energy efficiency | Lower | Higher |
Safety | Higher risk | Lower risk |
Reactive maintenance works for:
- Cheap, easy-to-replace items
- Non-critical equipment
- When downtime isn't costly
Planned maintenance is best for:
- Critical assets
- When downtime is expensive
- Safety-critical systems
Most facilities use a mix of both approaches. New tech like AI and IoT is making planned maintenance easier and more effective.
Companies using planned maintenance see:
- 15% less downtime
- 87% fewer defects
- Lower long-term costs
The best strategy depends on your specific assets and business needs.
What is Reactive Maintenance?
Reactive maintenance is simple: fix things when they break. No schedules, no check-ups. Just wait for problems and solve them.
It's also called "run-to-failure" maintenance. Think of it like waiting for your car to break down before taking it to the garage. You're not preventing issues, you're reacting to them.
When to Use Reactive Maintenance
Reactive maintenance isn't always bad. It can work for:
- Cheap equipment
- Non-critical assets
- Items that don't affect production or safety much
For instance, a small office might use it for printers. One breaks? They fix it. No big deal.
Types of Reactive Maintenance
There are four main types:
1. Emergency Maintenance
This is the "fix it NOW" type. It's for urgent issues that could cause safety problems or halt operations.
2. Breakdown Maintenance
This covers repairs on equipment that's stopped working, urgent or not.
3. Corrective Maintenance
This is fixing a problem early, before the equipment fails completely.
4. Deferred Maintenance
Sometimes, you spot an issue but fix it later. It can save time and money short-term, but might cause bigger problems later.
Here's a quick comparison:
Type | Urgency | Planning | Example |
---|---|---|---|
Emergency | High | None | Fixing a burst pipe in a factory |
Breakdown | Medium | Minimal | Repairing a stopped conveyor belt |
Corrective | Low | Some | Lubricating a squeaky machine part |
Deferred | Very Low | Scheduled | Postponing a minor repair until a quiet period |
Reactive maintenance isn't always best. A Plant Engineering study found 61% of manufacturing facilities use it. But this can lead to unexpected downtime and higher costs long-term.
"The manufacturing industry loses an average of $50 billion each year due to unplanned downtime." - Aberdeen
This huge figure shows why many companies are moving away from purely reactive strategies. They're starting to mix reactive maintenance with more proactive approaches to keep things running smoothly.
What is Planned Maintenance?
Planned maintenance is like giving your equipment regular check-ups. Instead of waiting for things to break, you take care of them before problems start.
It's similar to servicing your car on schedule, not waiting for the engine to fail.
Planned maintenance includes:
- Regular inspections
- Scheduled repairs
- Part replacements
- Performance checks
The goal? Less downtime, longer-lasting equipment, and fewer emergency fixes.
Types of Planned Maintenance
There are three main types:
1. Preventive Maintenance
This is the most common. It's based on time or usage, regardless of condition.
Example: Changing your car's oil every 5,000 miles.
2. Predictive Maintenance
This uses data to predict when maintenance is needed.
Think of sensors on a factory machine detecting unusual vibrations before a breakdown.
3. Condition-Based Maintenance
Similar to predictive, but triggered by specific conditions.
For instance, replacing HVAC filters when they're dirty, not on a fixed schedule.
Here's a quick comparison:
Type | Trigger | Example |
---|---|---|
Preventive | Fixed schedule | Monthly equipment check |
Predictive | Data-driven forecast | Replacing parts based on performance |
Condition-Based | Specific asset state | Lubricating when friction increases |
Planned maintenance isn't just about fixes. It's about better performance and lower costs.
UpKeep says businesses can save up to 18% with preventative maintenance instead of reactive approaches.
Deloitte reports predictive maintenance can cut breakdowns by 70% and boost equipment uptime by 10-20%.
"The manufacturing industry loses an average of $50 billion each year due to unplanned downtime." - Aberdeen
This huge number shows why many companies are moving towards planned maintenance.
With planned maintenance, businesses can:
- Dodge surprise costs
- Work more efficiently
- Meet safety rules
- Make equipment last longer
While it needs more planning upfront and might cost more initially, planned maintenance pays off. It cuts down on expensive replacements and helps equipment last longer.
Reactive vs Planned Maintenance
Let's compare reactive and planned maintenance:
Aspect | Reactive Maintenance | Planned Maintenance |
---|---|---|
Timing | Fix when broken | Scheduled in advance |
Cost | Low upfront, high long-term | High upfront, low long-term |
Downtime | Unpredictable, often long | Minimal, scheduled |
Asset lifespan | Shorter | Longer |
Energy efficiency | Lower | Higher |
Safety | Higher risk | Lower risk |
Reactive maintenance is "fix it when it breaks". It's simple but can lead to costly repairs and surprise downtime. Planned maintenance involves regular checks to prevent breakdowns.
How It Affects Your Business
Your choice between reactive and planned maintenance can make or break your daily operations:
1. Downtime
Reactive maintenance? Expect longer, surprise downtime. A manufacturing plant could lose a whole day's work because a machine suddenly died.
Planned maintenance? You schedule downtime when it's convenient. Less disruption, more control.
2. Money Matters
Think reactive maintenance is cheaper? Think again. Emergency fixes and lost production add up fast.
Planned maintenance spreads costs out. It's like a savings plan for your equipment. UpKeep says businesses can save up to 18% by preventing issues instead of reacting to them.
3. People Power
Reactive maintenance is like firefighting. Your team drops everything to fix urgent problems. Hello, overtime and stress!
Planned maintenance? It's like having a game plan. You know who's doing what and when. No surprises.
4. Safety First
Sudden breakdowns from reactive maintenance can be dangerous. They might even put you on the wrong side of safety rules.
Planned maintenance keeps your equipment in shape. It's safer for everyone and helps you follow the rules.
5. Energy Bills
Poorly maintained equipment guzzles energy. That means bigger bills and a not-so-green footprint.
Regular maintenance keeps things running smoothly. Your wallet (and the planet) will thank you.
Pros and Cons of Reactive Maintenance
Reactive maintenance means fixing stuff when it breaks. Simple, right? But it's not all smooth sailing. Let's look at the good and bad:
Pros | Cons |
---|---|
Cheaper upfront | Costs more long-term |
No complex planning | Surprise breakdowns |
OK for non-critical gear | Equipment dies faster |
Fewer maintenance staff | Safety risks |
More time for other work | Higher energy bills |
The Good Stuff
1. Cheap to start: You only pay when things break. Sounds budget-friendly, doesn't it?
2. No big plans needed: No fancy schedules or resource allocation. Just fix it when it breaks.
3. Works for some gear: For that coffee machine in the break room? Yeah, wait till it conks out.
The Not-So-Good Stuff
1. Ouch, the long-term costs: Emergency fixes? They'll drain your wallet. Aberdeen Group says surprise downtime can cost up to £200,000 per hour. Yikes.
2. Surprise, surprise: Equipment fails, production stops, business lost. Not fun.
3. Gear gets grumpy: No TLC means machines wear out faster. Hello, frequent replacements.
4. Safety first? Not really: Sudden breakdowns can be risky for workers and might break safety rules.
5. Energy hog: Poorly maintained equipment? It's like leaving the fridge door open. Your energy bills will show it.
"Reactive maintenance alone? It's like only going to the dentist when your tooth falls out."
Most businesses shouldn't ONLY use reactive maintenance. Mix it up. Use reactive for easy-to-replace stuff, but plan ahead for the important gear.
Think of a factory: reactive for light bulbs, planned maintenance for the big, expensive machines. Smart, right?
Pros and Cons of Planned Maintenance
Planned maintenance is more than just fixing things. It's a strategy that can impact your business. Let's look at the ups and downs:
Pros | Cons |
---|---|
Long-term cost savings | High initial costs |
Longer equipment life | Needs detailed planning |
Lower energy waste | Possible over-maintenance |
Safer workplace | Can't stop all breakdowns |
Fewer disruptions | Requires ongoing effort |
The Good Stuff
1. Money saver: Upfront costs? Yes. But here's the deal: every £1 spent on planned maintenance saves you up to £5 on surprise repairs. That's a 400% return!
2. Equipment longevity: Regular check-ups keep your gear running smoothly. It's like a spa day for your machines.
3. Lower energy bills: Well-maintained equipment runs more efficiently. Simple as that.
4. Safety boost: Planned maintenance catches issues before they become hazards. It's about keeping your workplace safe.
5. Smoother operations: Fewer surprise breakdowns mean less scrambling and more planning.
The Not-So-Good Stuff
1. Initial costs: Starting a planned maintenance program isn't cheap. You need tools, training, and time.
2. Planning challenges: It's not a wing-it situation. You need schedules, checklists, and tracking systems.
3. Over-maintenance risk: Sometimes you might check equipment that doesn't need it. It's like going to the doctor when you're healthy.
4. Not foolproof: Even with great planning, some breakdowns are unavoidable. You'll still need some reactive maintenance.
5. Ongoing work: Planned maintenance needs constant attention and tweaking. It's not set-and-forget.
"Only about 10% or less of industrial equipment ever truly wears out from proper use, meaning 90% of mechanical failures are due to preventable problems."
This stat shows why planned maintenance matters. It's about stopping problems before they start.
Cost Factors
Money matters when it comes to maintenance. Let's look at reactive vs planned maintenance costs:
Short-term vs Long-term Costs
Cost Factor | Reactive Maintenance | Planned Maintenance |
---|---|---|
Upfront costs | Low | High |
Emergency repairs | High | Low |
Equipment lifespan | Shorter | Longer |
Energy efficiency | Lower | Higher |
Downtime costs | High | Low |
Reactive maintenance seems cheaper at first. But it's like buying cheap shoes - you pay more over time.
The Hidden Costs of Reactive Maintenance
Reactive maintenance comes with hidden costs:
- Emergency repairs cost more
- Downtime loses money
- One broken part can damage others
- Poorly maintained equipment wastes energy
- Equipment doesn't last as long
The U.S. Department of Energy found reactive maintenance can cost 12-18% more than planned maintenance.
The Long-term Savings of Planned Maintenance
Planned maintenance costs upfront but saves money:
- You can budget for it
- Equipment runs more efficiently
- Your gear lasts longer
- You have fewer breakdowns
- You can schedule maintenance at convenient times
Some businesses cut energy bills by up to 40% with planned maintenance.
"Every dollar invested in preventive or predictive maintenance saves up to five dollars on unforeseen expenses."
This industry research shows the value of planned maintenance. It's like the saying: a stitch in time saves nine.
Making the Right Choice
Choosing between reactive and planned maintenance depends on your situation:
- Critical equipment: Always use planned maintenance
- Less important items: Mix reactive and planned maintenance
- Tight budget: Start with basic planned maintenance and build up
Effects on Facility Performance
Maintenance choices can make or break a facility's performance. Let's see how reactive and planned maintenance impact downtime, productivity, and equipment reliability.
Downtime and Productivity
Reactive maintenance often means more downtime. When equipment breaks unexpectedly, it can stop operations cold. This isn't just a small problem - it can mess up entire production schedules.
Planned maintenance, though? It keeps things running smoothly. By fixing issues early, facilities avoid sudden shutdowns.
Here's a quick comparison:
Factor | Reactive Maintenance | Planned Maintenance |
---|---|---|
Downtime | More frequent, unexpected | Less frequent, scheduled |
Productivity | Often disrupted | More consistent |
Cost of repairs | Higher due to emergencies | Lower due to prevention |
Equipment Reliability
Think of planned maintenance as a health check-up for your equipment. It spots wear and tear before things break down. The result? Machines last longer and work better.
Reactive maintenance is tough on equipment. Waiting for something to break before fixing it? That's a recipe for more damage.
Fun fact: 88% of industrial facilities use preventative maintenance. Why? Because it works.
Real-World Impact
Let's talk numbers:
"Businesses can save up to 18% by using preventative maintenance instead of reactive." - UpKeep
"Predictive maintenance can cut breakdowns by 70% and boost equipment uptime by 10-20%." - Deloitte
These aren't just stats. They're real money saved and more efficient operations.
Safety and Energy
Reactive maintenance can be risky. Sudden equipment failures? They can put workers in danger. Planned maintenance keeps things safer by tackling potential hazards early.
Well-maintained equipment is also more energy-efficient. That means lower bills and a smaller carbon footprint. Reactive maintenance often leads to equipment wasting energy and money.
The Bottom Line
Reactive maintenance might seem cheaper at first, but it costs more long-term. Planned maintenance is an investment that pays off through better performance, reliability, and safety.
As one facility manager put it:
"Switching to planned maintenance was like night and day. Our downtime dropped, productivity went up, and we're spending less on emergency repairs."
Picking the Right Maintenance Approach
Choosing between reactive and planned maintenance isn't simple. It depends on your facility's specific situation. Here's how to decide:
Assess Your Assets
Look at your equipment:
- How important is it to your operations?
- What happens if it breaks down unexpectedly?
- How old is it?
A hospital's backup generator needs planned maintenance. An office coffee machine? Reactive might be fine.
Budget Considerations
Planned maintenance costs more upfront but can save money over time. Reactive maintenance seems cheaper but can lead to expensive emergencies.
Maintenance Type | Upfront Cost | Long-term Cost |
---|---|---|
Reactive | Low | High |
Planned | High | Lower |
Resource Check
Do you have the people and tools for regular checks? If not, you might have to stick with reactive maintenance for now.
Industry Rules
Some industries have strict maintenance rules. For example, facilities handling hazardous materials must follow specific practices and keep detailed records.
Use Your Data
If you have maintenance records, use them. They can show which approach works best for different equipment.
Mixing It Up
Most facilities do best with a mix of both approaches:
1. Prioritise your assets
Use planned maintenance for critical equipment. Reactive might be okay for less important items.
2. Start small with planned maintenance
Begin with your most important equipment. Expand as you see benefits.
3. Stay flexible
Even with a planned approach, keep some budget for unexpected issues.
4. Use tech
Maintenance software can help. For example, eWorkOrders CMMS lets you schedule routine checks and handle unexpected issues in one place.
5. Keep reviewing
Regularly check how your maintenance strategy is working. Be ready to change based on results.
Overcoming Implementation Hurdles
Switching to planned maintenance isn't always easy. Here's how to tackle common challenges:
Lack of Management Support
No backing from the top? Try this:
- Show reactive maintenance costs
- Present ROI for planned maintenance
- Suggest a small-scale test
Incomplete Asset Information
Can't plan without knowing what to maintain. Here's what to do:
1. Create an asset list
Include equipment specs and maintenance instructions.
2. Assess asset condition
Check repair history, operating hours, and expected lifespan.
3. Develop maintenance checklists
Make tasks clear and standard.
Resistance to Change
Staff might push back. To help:
- Involve maintenance teams in planning
- Train on new procedures
- Show how it makes their jobs easier
Resource Constraints
Limited staff or budget? Consider:
- Start with critical assets
- Use free maintenance software
- Expand as you see benefits
Scheduling Conflicts
Balancing maintenance and production? Try:
- Plan weeks ahead
- Coordinate with production
- Use a CMMS to optimise
Measuring Effectiveness
Track these:
- Planned tasks completed on time
- Equipment downtime before and after
- Review and adjust regularly
Technology Challenges
New software can be tough. To help:
- Choose user-friendly systems
- Provide hands-on training
- Start basic, add features later
Technology in Maintenance
New tech is shaking up maintenance. Let's see how software and data tools are boosting efficiency.
Smart Systems
Computerised Maintenance Management Systems (CMMS) are game-changers. They help teams:
- Manage work orders
- Track spare parts
- Plan preventive maintenance
- Access info on the go
CMMS cuts paperwork and improves task assignment. Even small businesses can use cloud-based options now.
AI and Machine Learning
AI and Machine Learning are joining the maintenance crew. They're all about predictive maintenance:
1. Sensors collect machine data
2. AI analyses it
3. System flags potential issues
4. Teams fix problems early
This approach saves money and time. General Motors cut unexpected downtime by 15%, saving £16 million yearly in maintenance costs.
Internet of Things (IoT)
IoT devices are like chatty sensors. They keep tabs on machines 24/7.
IoT helps with:
- Temperature control
- Smart lighting
- Machine health checks
These sensors spot issues fast, often before damage occurs.
Impact on Maintenance Work
Old Way | New Way |
---|---|
Fix when broken | Prevent breakdowns |
Guess maintenance timing | Use data to decide |
Hunt for info | Info at your fingertips |
React to problems | Plan ahead |
Real Results
Companies using these technologies see:
- Up to 20% lower maintenance costs
- Up to 50% less unplanned downtime
- Equipment lasting up to 25% longer
What It Means for Teams
For maintenance workers, this tech brings:
- More informed decisions
- Fewer emergencies
- More planned work
- Better safety
Looking Ahead
We can expect:
- Sharper breakdown predictions
- Self-improving systems
- Smarter energy management
The future of maintenance? Proactive, not reactive. With the right tech, teams can keep things humming and save cash.
Real-World Examples
Let's see how companies use reactive and planned maintenance, and what they've achieved.
Frito-Lay: Crisp Production
PepsiCo's Frito-Lay plant in Fayetteville, Tennessee, uses vibration readings and ultrasound checks to spot issues early. The result? Just 0.75% year-to-date equipment downtime and 2.88% unplanned downtime.
Noranda Alumina: Bearing Benefits
Noranda Alumina's Louisiana plant changed their lubrication approach. In two years, they saw:
- 60% fewer bearing changes
- £720,000 saved
- Less downtime
A small change in planned maintenance led to big savings.
SDG&E: Predicting Problems
San Diego Gas & Electric used machine learning to predict T-splice failures. They:
- Fixed issues before they caused problems
- Extended the program to other assets
- Used AI to check millions of photos for equipment damage
SMRT Trains: AI on Track
Singapore's SMRT Trains Ltd. used AI for maintenance. They achieved:
- One million mean kilometres between failures across all lines
- Less manual planning time
- Fewer maintenance train trips
FORTRUST: Software Switch
FORTRUST, a data centre company, moved from Excel to maintenance software. This led to:
- 30% less inventory spend over 5 years
- 14 years of non-stop uptime for critical systems
Joe Harris, FORTRUST's critical systems lead, said: "The Excel spreadsheets just weren't cutting it."
Reactive Maintenance Still Matters
While planned maintenance is great, reactive maintenance has its place:
- A car breaking down needs immediate fixing
- A burst office pipe requires quick action
These situations show why having a reactive maintenance team ready is crucial.
What's Next in Maintenance
Maintenance is changing fast. New tech is making it easier to spot issues before they happen. Here's what's coming:
AI and Machine Learning
These tools are reshaping maintenance. They can:
- Find patterns in machine data
- Predict breakdowns
- Help schedule maintenance
GE uses AI to monitor jet engines. They fix issues before planes need to stop flying.
Internet of Things (IoT)
IoT devices are smart sensors. They watch machines and send data back. This helps maintenance teams:
- Know exactly what's wrong
- Fix things faster
- Avoid checking machines that are fine
Siemens uses IoT on wind turbines. They spot wearing parts before they break.
Maintenance 4.0
This combines all these new tools. It's about:
- Using data for better decisions
- Fixing things pre-emptively
- Cutting repair costs
A food company tried this and saw:
- 25% better machine performance
- 30% less spent on maintenance
What This Means for Maintenance Teams
1. New skills needed
Workers will need to learn:
- How to use new software
- Understanding machine data
- Working with AI tools
2. Better planning
Teams can:
- Fix things during downtime
- Order parts in advance
- Spend less time on emergencies
3. Fewer surprises
With these tools, expect:
- Less unexpected downtime
- Fewer big breakdowns
- More time to improve things
Challenges Ahead
There are some hurdles:
- Cost: New tech can be pricey
- Learning curve: It takes time to adapt
- Data concerns: Machine data needs protection
The Bottom Line
Maintenance is shifting from reactive to predictive. This means:
- Less machine downtime
- Lower long-term costs
- Happier customers
Brian Prendergast from JLLT says:
"AI insights enable teams to handle potential problems, like ordering replacement parts or equipment, before they grow in cost and complexity."
For maintenance teams, the future is about working smarter. It's an exciting time with new tools to make the job easier and more effective.
Conclusion
Picking between reactive and planned maintenance isn't simple. It depends on your assets and goals.
Reactive maintenance is good for:
- Cheap, easy-to-replace stuff
- Non-critical gear
- When downtime isn't a big deal
Planned maintenance works best when:
- Equipment is vital
- Downtime costs a lot
- Safety is crucial
Here's a quick look:
Aspect | Reactive | Planned |
---|---|---|
Initial cost | Lower | Higher |
Long-term cost | Often higher | Usually lower |
Downtime | More | Less |
Equipment life | Shorter | Longer |
Safety risks | Higher | Lower |
The stats are clear:
Companies using predictive maintenance saw 15% less downtime and 87% fewer defects.
Businesses relying on reactive maintenance faced 3.3 times more downtime than those who didn't.
In real life, a mix often works best. You might use planned maintenance for your main production line but reactive for office printers.